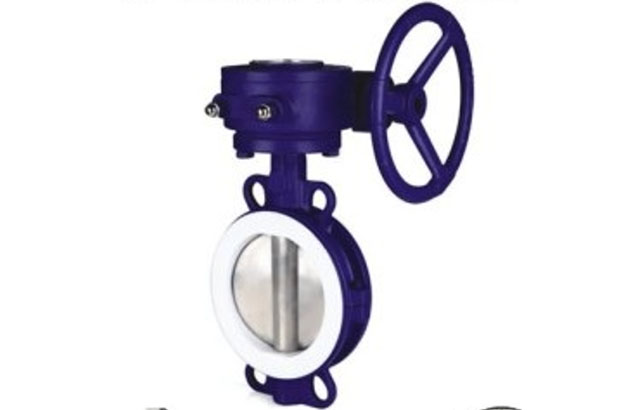
PTFE butterfly valve is to adapt to some corrosive environment with strong acid, strong alkali, petroleum, chemical, food and other special areas. The PTFE material has a strong anti-corrosion performance.In conventional conditions it can replace the stainless steel valve to save the cost.
1. Simple structure, small external size, short structure length, small volume, light weight, suitable for large diameter valves.
2. When fully open, the effective flow area of the seat channel is large and the fluid resistance is small.
3. Convenient opening and closing, fast, good adjustment performance.
4. The opening and closing moment is small, because the disc on both sides of the rotating shaft acts almost equally on the medium, and the direction of the torque is opposite, so the opening and closing needs less effort.
5. Sealing surface materials are generally rubber and plastic, so the low-pressure sealing performance is good.
6. Precision casting valve body. Qualified WCB material. Fine appearance, no trachoma.
7. The PTFE valve seat is integrally die-cast and then machined. To ensure density and tightness.
8. Double sealing rings design to avid the leakage from shaft.
9. Thickness of epoxy coating up to 250μm.
SIZE | F/F | PN10 | PN16 | Class150 | ||||
DN | NPS(INCH) | L | ΦD | ΦD1 | ΦD | ΦD1 | ΦD | ΦD1 |
50 | 2'' | 43 | 165 | 125 | 165 | 125 | 165 | 120.7 |
65 | 2 1/2'' | 46 | 185 | 145 | 185 | 145 | 185 | 139.7 |
80 | 3'' | 46 | 200 | 160 | 200 | 160 | 200 | 152.4 |
100 | 4'' | 52 | 220 | 180 | 220 | 180 | 220 | 190.5 |
125 | 5'' | 56 | 250 | 210 | 250 | 210 | 250 | 215.9 |
150 | 6'' | 56 | 285 | 240 | 285 | 240 | 285 | 241.3 |
200 | 8'' | 60 | 340 | 295 | 340 | 295 | 340 | 298.5 |
250 | 10'' | 68 | 395 | 350 | 405 | 355 | 405 | 362 |
300 | 12'' | 78 | 445 | 400 | 460 | 410 | 460 | 431.8 |
350 | 14'' | 78 | 505 | 460 | 520 | 470 | 520 | 476.3 |
400 | 16'' | 102 | 565 | 515 | 580 | 525 | 580 | 539.8 |
450 | 18'' | 114 | 620 | 565 | 640 | 585 | 640 | 577.9 |
500 | 20'' | 127 | 670 | 620 | 715 | 650 | 715 | 635 |
600 | 24'' | 154 | 780 | 725 | 840 | 770 | 840 | 749.3 |
1.Design and manufacture according to API609.
2.Face to face according to ANIS B16.10.
3.Flange drilling according to CLASS 150/PN10/PN16/10K.
4.Top flange drilling according to ISO 5211.
5.Pressure test according to API598.